化学职称论文发表还原铁粉生产应用
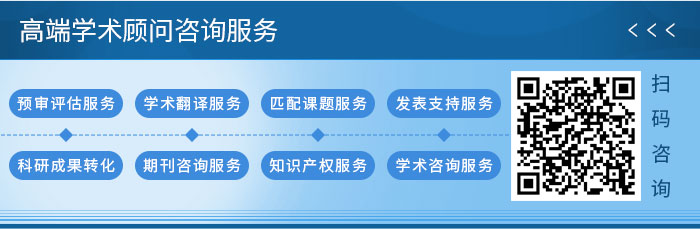
摘要:通过利用排除法查找造成海绵铁氧化的主要原因,并逐条落实改进措施,从而减少海绵铁氧化现象,提高了海绵铁生产质量。
关键词:海绵铁氧化,SiC罐密封,还原剂烧损,窑头、窑尾温度控制
1前言
泰东粉末自2006年建成投产以来,迅速成长并先后开发出多种产品系列,成为综合实力排名全国前列的知名厂家。不断改进和提高产品质量,占领产品质量制高点是企业持之以恒的发展道路和重要举措。其中降低海绵铁氧化,提高海绵铁质量就是重要举措之一。
2海绵铁氧化现象调查
我公司以轧钢除鳞铁粉为原料主体,配加还原剂焦末、石屑并装入SiC罐窑车,经预热、还原、冷却,制得还原铁粉的中间产品——海绵铁。在还原过程中,由于各种原因,海绵铁氧化现象较为严重,仅海绵铁头部氧化部分长度就达100~200mm,以单根海绵铁75kg计算,海绵铁头部氧化100~200mm,质量5~10Kg,整车质量损失100~200Kg,每月产量损失72~144吨。主要氧化部位在头部、SiC罐结合部两方面。海绵铁氧化头在一次粉破碎时必须去除,以消除对一次粉质量的影响。
3海绵铁氧化原因分析
海绵铁氧化是一个综合而复杂的过程,可能造成氧化的原因包括:装车工艺,还原工艺,进车工艺,窑炉性能等方面。下面我们就各种因素逐一分析。
3.1装车环节
从海绵铁头部氧化严重的现象来看,SiC罐封口料选择及封口方法不当,造成焦末烧损严重应是造成海绵铁氧化的主要原因之一。我们采用大小罐搭配的的组车模式,使得罐体之间密封不良,从而使罐内铁与氧气接触,造成了海绵铁氧化。
3.2窑炉性能及还原工艺因素。
隧道窑分预热段、还原段、冷却段三个部分,还原过程要在密封情况下进行。整个过程温度从窑头逐步升高,待还原完毕后迅速冷却,防止重新氧化。窑头温度不宜超过500℃,否则易出现进窑窑车SiC罐急热炸裂导致倒罐事故,并且在温度低于570℃时,还原反应主要体现为:
1∕4Fe3O4+C=3∕4Fe+CO △H298=167.59KJ∕mol
固体碳能直接还原铁的氧化物,由于固体与固体之间的接触面很有限,所以固-固反应速度慢;当温度高于570℃,反应按下述过程进行:
3Fe2O3+C=2Fe3O4+CO △H298=108.91KJ∕mol
Fe3O4+C=3FeO+CO △H298=194.26KJ∕mol
FeO+C=Fe+CO △H298=158.28KJ∕mol
反应剧烈,还原剂急剧减少(即所谓的烧损),罐顶密封性变差,使海绵铁尤其是海绵铁顶部氧化,我们实际操作中窑头温度在600℃左右,超过了工艺要求;在冷却段,还原工艺要求海绵铁还原完毕后温度迅速降低,一般要求窑车出窑温度不宜超过65℃,否则易出现海绵铁中的铁与空气中的氧结合,发生氧化反应。实际检测,出窑窑车温度在80℃左右,同样超出工艺要求,因此,窑头、窑尾温度过高也是海绵铁氧化的主要原因之一。隧道窑冷却段由薄壁间接冷却、水箱间接冷却、风箱间接冷却和风直冷组成,其中,窑车经过水箱间接冷却带时,海绵铁温度降低500℃左右,因此,水箱间接冷却是冷却段的关键环节,是降低窑车温度的最重要方式。
综上所述,SiC罐封口料选择及封口方法不当,罐体之间密封不良,窑头、窑尾温度过高是造成海绵铁氧化的主要原因。
4改进措施
4.1改善还原罐体连接密封
将用于SiC罐体密封的耐火泥,做对比试验:
实验一:将耐火泥用水在池内浸泡24小时,然后用于SiC罐体间密封,在1#窑46#窑车做实验,经预热、还原、冷却工艺,在三天的还原过程中,有几列密封泥脱落,由于罐体密封不良,造成部分海绵铁氧化。
试验二:将耐火泥用工业玻璃水以1:3的比例配比,在2#窑78#窑车试验,经相同工艺后,密封泥无脱落现象,整车海绵铁无氧化现象。
通过对比试验,在耐火泥中加入玻璃水,提高耐火泥的粘结性,在烧制过程中,提高了SiC罐与耐火泥的粘合度,使密封泥在高温过程中不易脱落,对SiC罐起到了良好的密封效果,有效解决了因罐体密封不良造成的海绵铁体氧化。
4.2改善还原罐口密封性
我们做如下对比试验:
选取一组待装窑车中4排罐,每排用不同封口料封口,出窑后测被氧化长度,结果如下:
试验证明,用第4种封口料所烧成的海绵铁氧化头最短,使用该种封口料,密封性增强,更符合海绵铁还原工艺要求。
4.3改善水冷箱循环性
隧道窑水冷箱采用循环水系统,与许多岗位共用一路水源作为冷却水水源。经测量,窑炉水箱的出水温度高达100℃,在此温度下出窑的海绵铁氧化现象频繁。水箱循环水进水管道为DN25,出水管道DN80,进出水量小,流动性差;水质硬度较高,在水箱内容易结垢,降低水箱冷却效果;每年进行一次水箱除垢,不能满足生产要求。
改进措施:⑴将进水管道由Φ25改为Φ50,Φ80出水管道由单个改为2个;⑵在循环水加软化除垢剂,改善水质硬化现象;⑶水箱除垢频次改为2次/年。
4.4加快风箱的风通传导
海绵铁车间密封过严,窑炉两侧温度高达65℃,导致风箱、薄壁冷却进风温度过高,冷却效果变差,窑车经此不能良好降温,出现海绵铁氧化频繁,海绵铁合格率降低。车间窑炉顶部只在窑头、尾设有引风口,而在温度最高的窑炉还原段无引风口,窑炉两侧空气流动性差,外部冷空气难以进入。
改进措施:⑴把车间顶部,窑炉还原段加装引风口,使窑头、尾引风口贯通。⑵拆除窑炉两侧部分采光板。⑶窑路中间加设通风机4台。通过以上措施,加快风通量,降低风箱和薄壁冷却段进风温度,加快窑内热传导,降低产品出窑温度。
5实施效果检验
5.1我们统计了10年3月~5月与09年同期海绵铁氧化头长度对比如下:
5.2我们同时对10年3月~5月与09年同期海绵铁氧化部分(氧化头与罐体结合部)氧化对海绵铁造成的产量损失统计如下:
通过以上效果图,我们可以得出,我们的改造达到并超过了海绵铁氧化头≤10cm,氧化造成质量损失≤50吨/月的预期目的,取得了理想而显著的效果。
6氧化部分的利用
根据海绵铁氧化程度(含氧量)的不同,我们分类存放,同时结合还原炉氢气还原所需碳氧成分动态平衡的原理,在生产一次粉所用海绵铁碳成分超标时适量加入,满足还原炉生产工艺需求。
7结语
我们对造成海绵铁氧化的原因进行了深入的研究,利用排除法找出了导致海绵铁氧化的主要原因,并逐条进行了相应的改造,经过分析、对比,我们的改造达到并超过了预期目的,取得了良好而显著的效果,为生产成分稳定、质量优良的还原铁粉奠定了坚实基础。同时,我们也看到,海绵铁氧化现象依然存在,在今后的工作中,我们将进一步强化生产过程质量控制,继续降低海绵铁氧化,为公司效益的提高做出更大的贡献。
《化学职称论文发表还原铁粉生产应用》