冶金职称论文发表复杂条件下异种钢材焊接
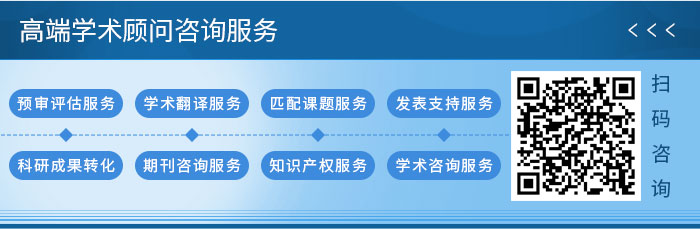
摘要:近年来,随着各类特大型复杂钢结构工程的涌现,普通的钢节点从制作、安装和受力角度,已不能满足工程需要。铸钢节点的应用很好的解决了这一难题,由于铸钢节点的复杂性,与之连接的杆件常为非铸钢不同材质,节点焊接难度也越来越大,特别是多杆件汇交形成的复杂节点;为满足节点构造要求和现场吊装要求,一些超长、超厚不同材质间焊接焊缝在施工现场进行焊接也就在所难免,而不同材质钢材的可焊性程度、焊接参数、焊接应力和变形控制等受现场条件、焊接位置及环境的影响,存在较多的不确定性因素,尚无成熟的规范及焊接工艺参数作参照。
关键词:复杂条件,异种钢材,焊接
一、前言
近年来,随着经济的发展、产钢量的提高,钢结构工程由于其优越的力学和环保节能等性能得到了迅速的发展,特别是2008年奥运会、2010年上海世博会等大型体育场馆、公共建筑、构筑物以及大跨度的厂房及市政公用工程等建设方兴未艾,给我国的钢结构设计施工带来了前所未有的挑战。
本文通过在 “黄金树”的现场焊接中,以56个超大型复杂多枝管状铸钢节点与大直径钢管的焊缝的成功焊接,总结了一整套关于异种材质、大直径钢管、全位置的现场焊接思路和方法。
二、技术控制重点、难点
2.1 异种材质焊接:铸钢件材质为ZG275-485H,无缝钢管材质为Q345B;
2.2 不等壁厚的对接焊:铸钢件壁厚为40mm,钢管壁厚为22mm或19mm;
2.3 焊接全部为高空管全位置焊接,相当部分接头焊缝呈斜向对接,仰焊部位较多;
2.4 空间狭窄材料厚度自12mm-22mm,“黄金树”的枝叉多达3至10个枝叉,需经常调整焊接作业位置和变更工艺参数,
2.5 防止出现焊接裂纹等质量问题:铸钢件接头必须连续完成,一气呵成,否则将有出现裂纹的危险;
2.6 焊接变形应严格控制:根本上减少焊接拘束,保证焊接应力释放自由,防止应力受约束过大,导致树结构整体变形过大。
三、适用范围
不同材质、不同壁厚钢材现场全位置焊接。
四、工艺原理
通过对“黄金树”整个模型的分析,结合构件安装校正的数据,制定和优化焊接方案,通过对实验节点的现场焊接,掌握实际焊接参数,制订焊接工艺指向书,确定焊接参数。现场采用优化焊接顺序,对称焊接,反焊接变形措施,一次完成单个铸钢节点的焊接。通过观测焊后节点变形数据,确定下一节点的焊接顺序,从而完成整个“黄金树”节点的焊接,确保焊接质量的同时保证构件的变形在允许范围内。
五、工艺流程
分析结构,制订对策->制定焊接方案->焊接实验->确定焊接参数->分析节点、校正数据、确定焊接顺序->焊接前准备,焊缝坡口检查->焊缝预热->焊接->焊缝后热、保温->焊缝后热、保温->焊缝打磨伤->合格->记录、验收
六、施工要点
6.1 明确目标,制定对策
6.1.1分析复杂条件下异种钢材焊接难度所在,优化焊接工艺,从合理的施焊顺序入手,重点加强防温度散失、防大风、防潮温、防骤然降温等措施的有效设立。根本上减少焊接拘束,对预热、层温、后热、保温等各个有效环节予以保证焊缝质量。
6.1.2 提高技工焊接质量意识,加强焊接中行为和焊接结果监控。
6.2 焊接措施
6.2.1焊接要求
铸钢件与钢管的对接为全位置焊接。坡口形式为带内衬管V形坡口(此坡口形式可减少焊缝断面,减小根部与面缝部收缩差,防止由于焊接应力过度集中在近面缝区产生撕裂现象)。对接接头采用手工电弧焊焊接,焊条选用E—5015,直径选用Φ3.2mm~4mm。整个焊接过程须一次完成,严禁中途停焊,必须从组对、校正、复验、预留焊接收缩量、焊接定位、焊前防护、清理、预热、层间温度控制、焊接、后温、保温、质检等各个工序严格控制,确保接头焊后质量达到设计要求及规范规定。
6.2.2 焊接变形控制
1、节点焊接顺序:从下向上,由中间向四周,尽可能减少焊接约束,保证焊接应力释放自由,防止应力受约束过大,导致树整体变形过大。
2、铸钢节点所有分枝与对接钢管安装、精校到位,方可施焊。
3、节点焊接顺序。
图6-2节点焊接顺序平面示意
4、节点分枝焊接顺序:
本工程节点分枝多:从3—10个分枝不等,其中431#节点分枝有10根,节点接头越多,相互影响越大。
节点分枝先焊后焊所存在的收缩差,对节点x、y、z值影响较大:影响到节点本身空间定位精度、影响到相关节点空间安装、影响到杆件的安装。
先粗杆(热输量大),再细杆,平面力求对称施焊。
根据节点焊前的测量的报告,制定每个分枝焊接顺序。
5、接头全位置焊接顺序
管对接后按天芯分两个半圆形焊接,都以仰焊部位起焊,以平焊部位收焊。
两个半圆分层对称施焊,控制焊接接头水平方向焊接变形。采用多层多道的对称焊接方法,减小焊接中变形。
6、接头反变形矫正
节点施焊后,必然产生向上微弯变形。
采取中性火焰后热进行反弯,上部加热面积小,下部加热面积大,从而恢复接头。
6.3 铸钢节点接头现场焊接工艺及试验
6.3.1 焊接工艺
1、 材质:铸钢材质为ZG275-485H,壁厚40mm;钢管材质为Q345B,壁厚22mm、19mm。
2、 焊口形式与数量:焊缝坡口形式为带内衬管V型坡口。共七个焊口:一根管径450mm管壁22mm、六根管径350mm,管壁19mm。
3、 焊接方法:采用手工电弧接
4、 焊材:本次工艺评定使用的焊材为E5015φ3.2-4.0mm焊条。
5、 焊接工艺评定试件的组对:组对要求达到无污物锈蚀、无缺损、错边。
6、 焊前铸钢件坡口检查。
7、 现场施焊:焊接工艺评定的焊接技工为专业焊工。
8、 焊缝检验
外观检验:焊波均匀,不得有裂纹、未熔合、夹渣、咬边、烧穿、弧坑和针状气孔等缺陷,焊接区无飞溅残留物。
无损探伤:对接焊缝试件的UT检验标准执行GB11345—89有关规定,检验结果必须符合GB50205—95表4.7.20I级标准。
6.3.2现场焊接工艺评定
通过进行铸件与树枝杆件进行多参数模拟焊接试验,以确定最佳的焊接参数及工艺措施;保障接头的焊缝致密度,力学性能指标及外观达到设计与规范要求,从而形成适合本工程的铸钢铸造与现场焊接工艺。
1、无损检测
X射线检测:检测焊缝内部是否存在超标或危害性缺陷,焊缝根部是否焊透、熔合。超声波检测:检测焊缝内部是否存在超标或危害性缺陷,焊缝根部是否焊透、熔合。磁粉检测:检测焊缝在表面、近表面是否存在裂纹等危害性缺陷。
2、里氏硬度检测:对焊缝及两侧热影响区和母材的硬度检测。
3、机械性能试验
对焊缝进行机械性能试验、评定,明确焊缝的性能是否达到设计要求。进行拉伸试验、冷弯试验、冲击试验,试验结果见表表6-3。试验结果表明:各项检测均到达设计与规范要求。
6.4 异种钢材现场焊接
6.4.1焊口清理与组对
组对前先采用锉刀、砂布、盘式钢丝刷,将铸钢件接头处坡口内壁15—20mm处仔细清除锈蚀及污物。坡口外壁自坡口边坡10-20mm范围也必须仔细除去污物,坡口的清理是工艺重点。由于铸钢件的表面光洁度较差,在组对前必须把凹陷处用角向磨光机磨平,坡口表面不得有不平整、锈蚀等现象。无缝钢管的对接处清理与铸钢件相同。组对时不得在铸钢件部位进行硬性敲打,防止产生裂纹。错口现象必须控制在规定允许范围内。
6.4.2 焊前检查
铸钢(ZG275-485(H))与钢管(Q345B)对接接头的焊前检查由专业技术人员检查,确认符合规程要求后,下达焊施指令,完善交接手续。
6.4.3 铸钢节点焊前预热
本工程采用的ZG275—485H铸钢件与Q345B无缝管材在焊接时对预热、层温、后温等要求非常高。故在进行预热处理时应严格执行下述要求:预热范围应沿焊缝中心两侧各100mm以内进行全方位均匀加热,当预热温度、范围均达到预定值后,恒温20~30分钟。温度的测试须在离坡口80~100mm处进行,采用红外线测温仪感应测温。热源采用氧—乙炔中性火焰,进行加热时至少使火焰焰蕊距管壁具有不小于100mm的距离且不时绕管运作,以免造成加热不均匀,单点温度过高而造成对铸钢件的损伤。6.4.4根部焊接
全位置管—管对接接头在焊接根部时,应自焊口的最低处中心线10mm处起弧至管口的最高处中心线超过10mm左右止,完成半个焊口的封底焊。另一半焊前应将前半部始焊与收尾处用角向磨光机修磨成缓坡状并确认无未溶合现象后,在前半部分焊缝上起弧,焊至前半部分结束处焊缝上,终了整个管口的封底焊接。由于本工程所使用的铸钢件接头处带有与铸件连为一体的管内垫板,故根部焊接只须注意衬板与无缝钢管坡口部分的熔合,并确保焊肉介于3.0mm~3.5mm之间。
6.4.5 填充层焊接
在进行填充焊接前应剔除首层焊道上的凸起部分与粘连在坡壁上的飞溅及粉尘,仔细检查坡口边沿有无未溶合及凹陷夹角,如有上述现象必须采用角向磨光机除去,不得伤及坡口边沿。焊接时注意每道焊道应保持在宽8-10mm、厚3-4mm的范围内。运焊时采用小8字方式,焊接仰焊部位时采用小直径焊条,仰爬坡时电流逐渐增大,在平焊部位再次增大电流密度焊接,在坡口边注意停顿,以便于焊缝金属与母材的充分熔合。每一填充层完成后都应做与根部焊接完成后相同的处理方法进行层间清理,在接近盖面时应注意均匀留出1.5-2mm的坡口深度,不得伤及坡口边,为面缝做好准备。
6.4.6 面层焊接
直接关系到焊接接头的外观质量能否满足质量要求,因此在面层焊接时应注意选用小直径焊条,适中的电流、电压值并注意在坡口边溶合时间稍长。水平固定口时不采用多道面缝。垂直与斜固定口须采用多层多道焊。严格执行多道焊接的原则,焊缝严禁超宽(应控制在坡口以外2~2.5mm内)超高(保持左0.5~3mm)。
重点:
1、在面层焊接时为防止焊道太厚而造成焊缝加强面超高应选用偏大的焊接电压进行焊接。
2、 为控制焊缝内金属的含碳量增加,在焊道清理时尽量少使用碳弧气刨以免刨后焊道表面附着的高碳晶粒无法完全清除,致使焊缝内含碳量增加,出现延迟裂纹。
3、 为控制线能量,应严格执行多层多道的焊接原则,特别是面层焊接,焊道更应控制其宽度不得大于8-10mm。焊接参数应严格按规定热输入量。
4、 焊缝成型后要求均匀、圆滑过渡,饱满、无咬肉、无夹渣、无气孔、无裂纹。
6.4.7后热与保温
焊接节点完成后,为保证焊缝中扩散氢有足够的时间得以逸出及焊接收缩产生的应力得以释放,从而避免产生延迟裂纹出现。焊后必须立即进行后热、保温处理。后热时采用氧—乙炔中性焰在焊缝两侧各100mm内全方位均匀烘烤,并有意识将最后加热处放置在始焊处。经表面温度计在离焊缝80—100mm处测试达到200—2500C后用不少于4层石棉布紧裹并用扎丝捆紧,保温至少须达4小时以上,确保接头区域达环境温度后方能拆除。
6.4.8焊缝的无损检测
焊缝在外观检查合格的前提下,经焊后≥24小时冷却使钢材晶相组织稳定后,按图纸要求对焊缝进行超声波无损检测,执行GB-11345-89钢焊缝手工超声波探伤方法和结果分级,规定的检验等级并出具探伤报告。为确保铸钢件出现焊后撕裂现象的及时发现,将对具有代表性的重要承力节点进行跟踪复检、监控。监控点计划24小时进行一次,共约30天,每日均须出具复检结果。
七、主要机具、设备
CO2气体保护焊焊机5台,烤枪5把,CO2气体、氧气、乙炔若干,红外线测温仪2台。
八、劳动力配备
焊工10人,普工10人, 探伤2人, 测量4人
九、质量控制
9.1 预先试验:限定试件为429#铸钢节点,比例为1:1,通过对铸件与树枝杆件进行多参数模拟焊接与试验检测,以确定最佳的焊接参数及工艺措施。
9.2 过程控制:首先控制黄金树整体焊接变形:采取从下向上,由中间向四周焊接顺序,尽可能减少焊接约束,并制定每个节点的焊接顺序;控制节点各分枝焊接相互变形:先粗杆(热输量大),再细杆,平面力求对称施焊;根据节点焊前的测量的报告,调整节点每个分枝焊接顺序;控制单个接头焊接变形:管对接后按天芯分两个半圆形焊接,都以仰焊部位起焊,以平焊部位收焊。即按仰焊、仰立焊、立焊、立平焊、平焊等顺序焊接。同时采取接头反变形矫正措施。
9.3 焊后检验:对所有的焊缝进行100%的超声波探伤。
9.4 通过应力应变测试,对结构焊前、焊后、拆除胎架后引起的内力变化进行跟踪观测,并记录相关的数据,确保焊接引起的内力设计应力值。
十、安全注意事项
10.1由于现场为高空全位置焊接,必须搭设牢固的焊接平台,并设置安全网,施工人员必须按规定挂牢安全带。
10.2 注意防火,焊接前清理作业区易燃易爆物品,设置足够的灭火器和消防用水。
10.3 注意天气情况,密切关注天气预报,必要使设置防雨棚,以防焊接中途停顿。
十一、结语
“黄金树”结构,设计按照“树”的生长机理,由下至上按照主干、粗枝、中枝和端枝组成结构体系,多根钢管杆件以不同的角度汇交于一点,组成树形的空间三维体系,主干从一层6m标高开始为四根钢—混凝土柱结构,主干上伸出的枝用钢管做成。主干及各枝的连接处采用铸钢节点,铸钢节点为多根420mm和390mm大直径钢管直接汇交,随着树枝的生长,四个主干的支出的树枝钢管交错、汇集,最终在顶部形成一个整体屋盖,主杆件共计216根,连接黄金树端枝的构件作为主梁,在主梁的各面上设置次梁。两棵树最高点40m,投影面积约3400平方米,汇交节点共计67个,67个铸钢节点形状各异,没有两个是完全相同的,伸出的枝管数量由3个到10个不等。钢结构工程量约1200t。
经过对焊接环境的着意保护、焊接工艺优化和监控、焊接过程各道工序的有效制约,经过极严格的100%无损检测的检查,本工程焊缝一次合格率为100%。
本项目异种钢材复杂条件下焊接取得了成功,为建筑用铸钢在大型、复杂的钢结构建筑推广与应用创造了先河。
参考文献:
1、 戴为志,刘景凤 著《建筑钢结构焊接技术:“鸟巢”焊接工程实践》 化学工业出版社 2008-03-01
2、 张耀春著 《钢结构设计原理》 高等教育出版社; 第1版 (2011年1月1日)
《冶金职称论文发表复杂条件下异种钢材焊接》